Inventory management is the process of overseeing and controlling the ordering, storage, and use of a company’s inventory. This includes raw materials, components, and finished products, as well as the warehousing and processing of such items. Effective inventory management is crucial for ensuring business efficiency, cost control, and customer satisfaction.
Why is Inventory Management Important?
Cost Control: Proper inventory management prevents overstocking, which can lead to excess storage costs or losses due to obsolete products. Similarly, understocking can result in missed sales opportunities and unhappy customers. Striking the right balance is key to minimizing holding costs while maximizing sales.
Improved Cash Flow: Tying up too much cash in inventory can harm a business’s liquidity. Effective management helps optimize the flow of goods and prevents capital from being unnecessarily locked into unsold stock.
Customer Satisfaction: Inventory management ensures that products are available when customers need them, reducing lead times and backorders. A well-managed inventory system contributes to better service levels and customer retention.
Types of Inventory
There are several types of inventory that businesses need to manage, including:
Raw Materials: The essential components used in the production of goods.
Work-in-Progress (WIP): Partially finished products still undergoing the manufacturing process.
Finished Goods: Completed products that are ready for sale.
MRO Goods: Maintenance, repair, and operating supplies necessary for supporting the production process but not part of the final product.
Key Inventory Management Techniques
Just-In-Time (JIT): JIT is a strategy where inventory is ordered only as needed. This reduces holding costs but requires a highly responsive supply chain to avoid stockouts.
Economic Order Quantity (EOQ): EOQ is a formula used to determine the optimal order quantity that minimizes the costs of ordering and holding inventory. It balances the trade-off between ordering frequently and holding large amounts of stock.
ABC Analysis: This technique categorizes inventory into three groups (A, B, and C) based on their importance and value. Group A consists of high-value items with low sales frequency, while Group C includes low-value items that are sold more frequently. This helps focus attention on managing the most critical stock.
FIFO and LIFO: “First-In, First-Out” (FIFO) ensures that the oldest inventory is sold first, which is crucial for perishable goods. On the other hand, “Last-In, First-Out” (LIFO) assumes that the most recent inventory is sold first, which may be beneficial in industries with rising costs.
Safety Stock: Safety stock refers to the extra inventory kept on hand to prevent stockouts caused by unforeseen demand or supply chain disruptions. Calculating the right amount of safety stock is crucial for minimizing risk without inflating holding costs.
Technology in Inventory Management
Modern inventory management heavily relies on technology to ensure real-time tracking and automation. Some key tools include:
Inventory Management Software: Systems like SAP, Oracle, or QuickBooks help businesses automate stock control, streamline purchasing, and track real-time inventory data. They also assist in forecasting future demand.
Barcoding and RFID: Barcoding and Radio Frequency Identification (RFID) systems help track products throughout the supply chain. These technologies provide visibility into stock levels and locations, reducing errors and improving accuracy.
Cloud-Based Solutions: Cloud-based inventory management systems allow businesses to monitor their inventory from anywhere, offering flexibility and scalability for growing companies.
Challenges in Inventory Management
Demand Variability: Predicting customer demand can be difficult, especially in seasonal-industry industries. Poor demand forecasting leads to either excess inventory or stockouts.
Supply Chain Disruptions: External factors, such as supplier delays, natural disasters, or geopolitical events, can cause inventory shortages or delays and disrupt operations.
Obsolescence: Over time, certain products may become obsolete due to changing customer preferences or technological advancements. Managing this risk involves timely product rotation and clear planning for phasing out older stock.
Best Practices for Effective Inventory Management
Regular Audits: Conduct regular inventory counts, either manually or through automated systems, to ensure that your records match the actual stock on hand.
Demand Forecasting: Use historical data, market trends, and advanced analytics to forecast future demand accurately. This helps in planning inventory levels and minimizing both overstock and stockouts.
Vendor Relationships: Strong relationships with suppliers are crucial for managing lead times and ensuring the timely delivery of products. Transparent communication with vendors can help mitigate supply chain disruptions.
Inventory Turnover Ratio: Monitor your inventory turnover ratio, which measures how often inventory is sold and replaced over a given period. A high turnover ratio indicates efficient inventory management, while a low ratio suggests overstocking.
Conclusion
Effective inventory management is essential for the smooth operation of any business, whether it’s a small retailer or a large manufacturing firm. By balancing supply and demand, reducing excess stock, and improving cash flow, businesses can enhance profitability and ensure customer satisfaction. Embracing the right techniques and technology is key to overcoming the challenges of managing inventory in a dynamic market environment.
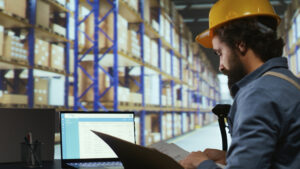
Export supervisor drafting billing for product logistics, managing shipping and delivery requirements. Factory operator reviewing dispatch reports for order submission and stock control.